|
10micron
GM2000 QCI German mount |
|
|
|
Especially in astrophotography the stability of a mount is hugely important. Given that I had some irresolvable technical problems with the previous mount, I finally chose a GM2000, the “bella macchina” from Italy. I came to this decision when I first saw the mount in action, used by a friend.
10micron manufactures these beautiful and highly precise mounts near Milan.
Two versions of the GM2000 are available. In the ultraport-version the DEC- and RA-part can be separated from each other. The axes in the monolith-version are fixed permanently. For an easier handling I have decided to purchase the separable ulraport-version. In this layout none of the parts is heavier than 15kg.
All parts are produced from milled aluminium and stainless steel. The construction is available with a red, blue or silver-grey anodised surface.
This mount can support masses of up to 40kg (photographical use). The typical periodic error is guaranteed to be +/- 3 arc seconds. |
|
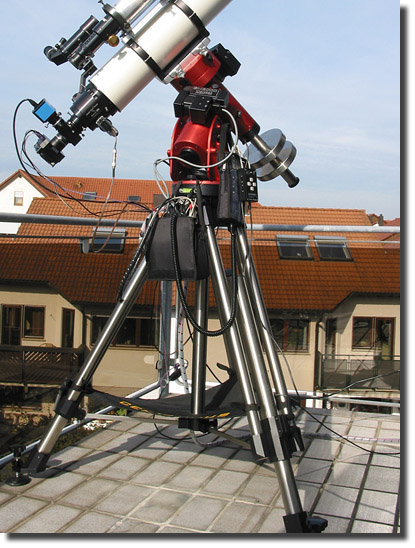
|
GM2000
on Centaurus Tripod
|
|
|
Mounting-Plate:
The diameter is 230 mm. The shank in the middle projects into the lower part of the mount and works as a bearing stud for the AZ-alignment. The tripod is equipped with a level which allows exactly and easily setting the stand horizontally.
|
|
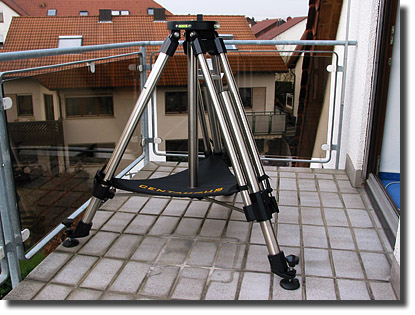 |
Centaurus stainless steel tripod:
The tripod's weight is of about 25 kg and the bearing force is 100 kg. I have never seen such a stable tripod before. This tripod is also available with carbon tubing. The latter weighs 10 kg less but is not as rigid as the steel version. |
|
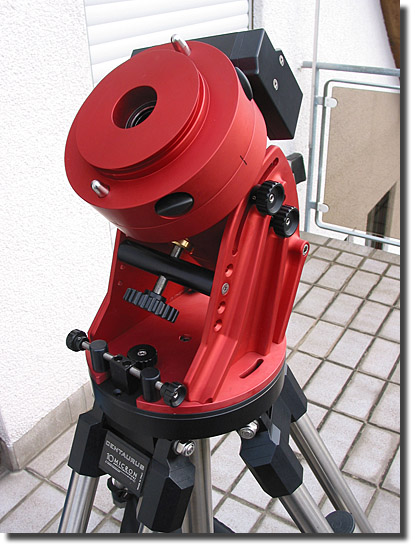
|
R.A. part:
As described in the beginning, the RA-part and DEC-part can easily be separated in the ultraport-version shown above. A revolving dovetail ring construction allows this. The two conical shanks can be used to centre the DEC-part when it is attached. If the DEC-part is set on roughly perpendicular, there will be no problem to fit the components accurately.
The image shows the collimation screw for AZ and Alt. All components are made up of aluminium and stainless steel. The screw axle clamp of the Alt-collimation can be set up in four different positions in such a way that pole heights of 22°-66° can be regulated.
|
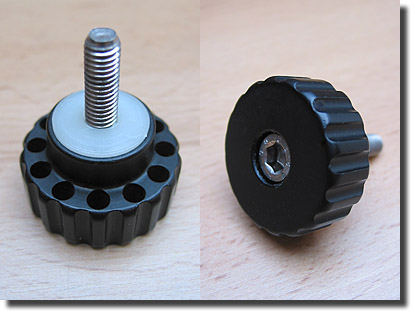 |
Even the control dial is completely made up of aluminium and hollow-drilled on the backside! The setscrew consists of stainless steel and has a hexagon socket.
|
|
|
The motor transmission units are completely housed in metal. The AC-servomotors are far ahead compared to usual step motors due to their absolutely uniform and smooth movement. A toothed drive belt transfers the force to a worm wheel with no backlash.
|
|
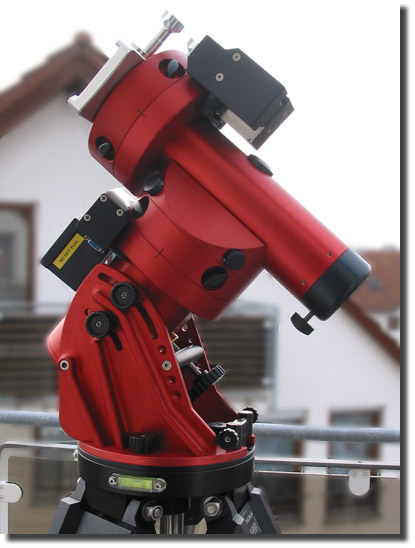 |
|
|
The GM2000 with its RA-unit set up. The bar with the counterweights can be fastened separately. It is precisely ground and slides into the adapter on the backside of the DEC-part with no vacuity. (Thanks to the bayonet) The axis clicks into place very closely-fitting and can be fixed with a screw.
|
|
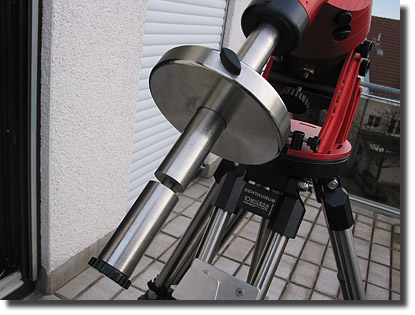 |
The counterweight bar measures 400 mm which is relatively long. It completely consists of massive stainless steel and has a diameter of 40 mm. Since the overall length disturbed me on my balcony, I had the bar cut into two pieces. The lower end can be screwed on with a M16 thread when needed. This optional extension has turned out to be very handy.
|
|
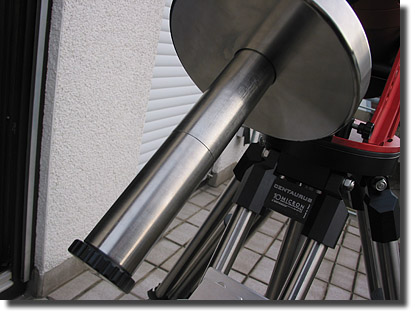 |
The extension for the counterweight bar.
Counterweights are available with masses of 6 kg and 12 kg. |
|
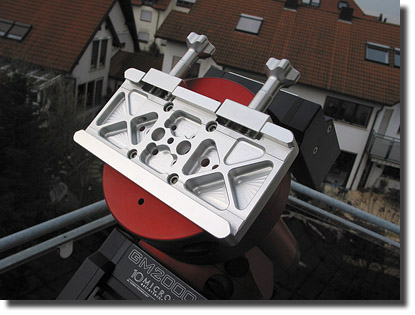 |
Although the original Baader 2” prism-adapter (compatible with Losmandy) was robust enough, I replaced it with a high-quality model from BT-Technologies. In order to increase the bearing area I had the bottom side of the clamp milled. In addition I had nearly all the dovetail removed on one side so that the dovetail supporting the heavy telescope doesn’t need to be threaded completely. Once 2/3 of the telescope have been put on the lower part of the dovetail, the telescope can be raised up and moved a little backwards. Only on the backmost part the dovetail is present on both sides so that the telescope cannot pivot out any more. In a final step the clamp jaw must be tightened with the T-screw. The clamp jaws are spring borne and can slide on the positioning dowels with virtually no vacuity.
|
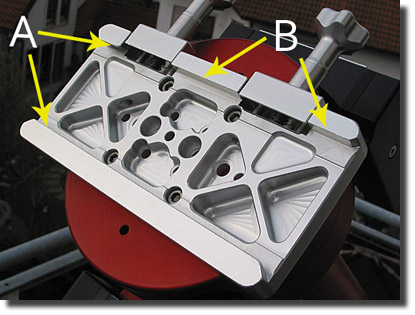 |
A: dovetail present
B: dovetail removed |
|
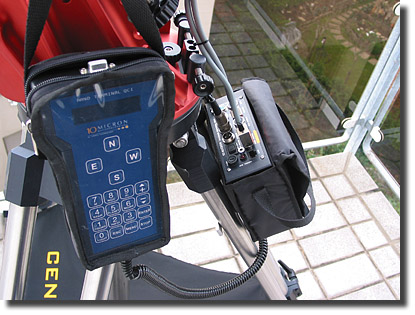 |
Control of the mount
Included in delivery of the GM2000 there is an autonomous control unit. It consists of the control itself (right-hand on the image) and a hand box with a double-spaced display (blue on the image). A µ-processor with Linux system software operates the control unit. The control unit needs approx. 1min to boot the system software.
Two different electronic engineering layouts are available: either as a box in a handy bag (see image) or integrated in the column as an intermediate piece between column and mount. Both versions have their pros and cons.
I have settled on the bag version because I don’t want to leave damageable technical equipment outdoors when I don’t use it.
Given that the entire control system is embedded in the electronic bodywork, no additional PC is needed for the goto-mode of the GM2000.
Especially the firmware offers a number of highlights:
The alignment of the mount (initialisation on the actual sky) can be carried out with different sophisticated algorithms. Especially the 3-star method is very recommendable. At first, the mount must be aligned roughly on the polar star. In this process, the mount navigates the telescope to three arbitrary stars listed on a schedule. Even if it is only possible to observe a small section of the sky there will still be available enough stars for reference to choose from. The selected stars must be brought exactly in the middle of the cross-hair eyepiece and can be confirmed with the enter-key.
At that stage the really genial part follows: the alignment of the pole
After the alignment has taken place, the mount can now be aligned WITHOUT pole finder and WITHOUT direct visibility of the polar star. In the accordant mode of the control system you can just simply choose another reference-star from a list and the mount navigates to this star. To bring this reference-star in the middle again, you only have to operate the AZ and Alt-adjustment-device. In this process the mount is simply and accurately aligned to the pole. The result is striking exact. The pole finder scope is definitely not necessary.
To increase the aiming accuracy the steps above can be applied to a larger number of stars (refinement). |
|
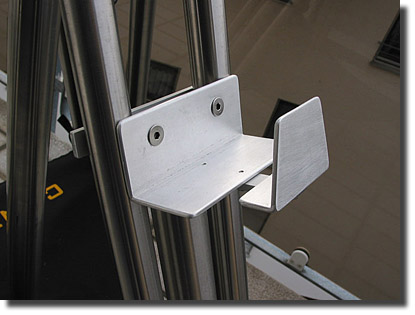 |
Self built retainer on the stand for holding the electronics box. Unfortunately 10micron doesn’t offer any serial solution for this purpose. |
|
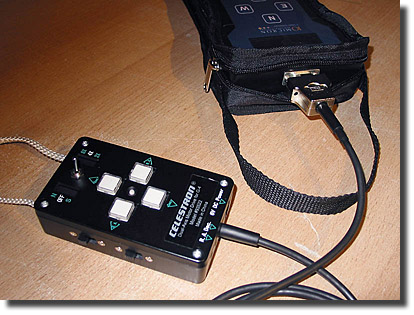 |
Tuning
The keys on the hand box are all illuminated but not very elevated. Therefore it is fairly difficult to operate them without looking. The keys cannot be sensed very easily and confusion of different keys may occur.
For this reason I have built another hand box, which only has the four direction keys and a tappet switch for adjusting the slew-speed. By using the buttons on the side, the direction of the control keys can be inverted. This turns out to be very handy when operating the mount. The little extra hand box can be connected after installing a 9-pole sub-D jack. The correct connections on the plastic foil keyboard can be found by using a circuit indicator. The keys of the extra hand box must simply be connected in parallel to the keys on the plastic foil keyboard. |
|
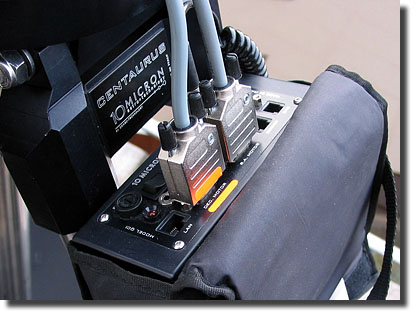 |
A little imperfection: the connector casing of the motor cables (15-pole sub-d) is originally made of cheap plastic. However, in specialist electronic shops there are available connector casings of die cast metal. The connector casings can be substituted easily and no brazing is necessary to fix the metal cases.
|
|
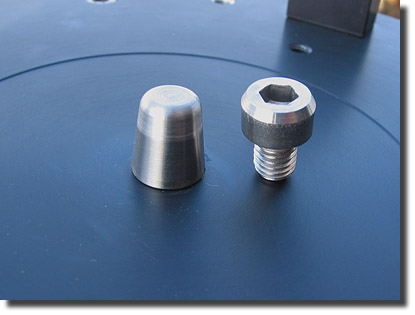 |
The original centring shank had slightly too much vacuity in the bore of the RA-unit (a few 1/10mm). It is a simple M8-allen screw. To increase the accuracy when re-attaching the RA-unit, I had spun an exactly fitting shank of stainless steel. |
|
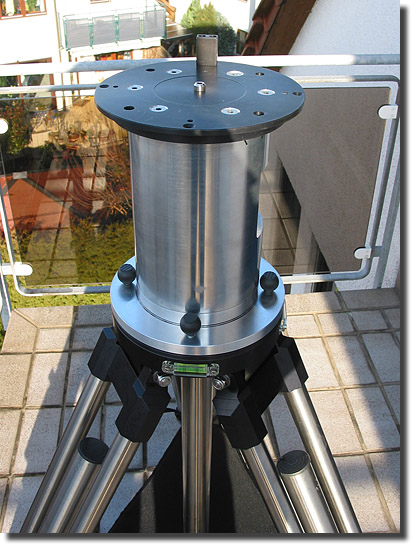 |
Extension of the column
My friend Kurt has wounded this wonderful elongation for the column from a thick aluminium tube. In praxis it is much easier to put on the extension instead of extracting all the tripod legs and levelling al the mount again. The additional height due to the elongation is 285mm. The wall thickness of 15mm leads to outstanding stability. The elongation is very handy especially for the use for visual purposes with a refractor in proximity of the zenith.
|
|
|
The following connections can be used at the control logic unit:
- RA- and DEC-motors
- Auto guider
- Serial interface to the PC (control is possible with a number of planetarium programms)
- LAN-interface (Ethernet to the router or PC)
- GPS-module (very handy for exact position and time)
- Hand box
- Power supply (24V)
- External contact to switch the control on and off
|
|
My personal conclusion:
The GM2000 represents a perfect solution for everybody who is looking for the ultimate and uncompromising mount. The mechanical layout, the software, stability and precision of operation all contribute to an overall concept that sets new benchmarks. Apart from the small modifications mentioned above I could not imagine any improvements for this great mount. Solely the precious finish in anodized red is a feast for the eyes.
Since I have started to use the GM2000 for photography purposes I can use 100% of my raw images!
When I had accurately aligned the telescope I could get clear images with no deformation of the stars even without any auto guide and exposure times of 10min. (1000 mm focal length)
The only drawback is the astronomically high price – however, in my opinion this Italian beauty is worth every cent!
If there is something like a final solution, the GM2000 can be considered to be one.
|
|
Technical
data:
- manufacturer: 10micron
COMEC Technology
- description: GM2000 QCI Ultraport
- weight of DEC-unit: 13.5 kg
- weight of RA-unit: 15.1kg
- total weight: 28.6kg (only axes, no counterweight)
- maximal support force: 50kg (40kg photographic suggested)
- counterweight bar: diameter 40mm, 4kg
- counterweights: available with masses of 6kg and 12kg
- precision: +/- 3” (PEC possible)
- axes: 50mm, steel
- worm gears: base in aluminium, gear ring in bronze, diameter 172mm
- worm: 24mm, steel
- guiding speed: 0.5x (fixed value)
- goto-speed: up to 8°/sec
- motors: AC servobrushless F.I.S.
- adjustable pole height: 22°-66°
- pole finder: available as an optional, not necessary
- GPS: optional GPS-module available
- Tripod: Centaurus stainless steel (25kg) or Carbon (ca. 16kg), maximal support force 100kg
- Power supply: 24V / max 1.7A (0.6V with sidereal tracking)
- Transport bag: available as an optional
|
|